As battery electric powered vehicles gain a larger share of the market, the technology shift from internal combustion engines to high-voltage (HV) batteries may require a different approach for many repair and refinish operations. Longstanding repair procedures may no longer align with the advancements incorporated in new vehicles. One such procedure that may require rethinking is how the applied refinish system is cured.
The elevated temperatures commonly used when force-drying an automotive refinish system have the potential to cause thermal damage to the HV battery. The possibility of booth curing temperature being too high is something that technicians rarely, if ever, contemplated in the past. HV batteries that store the energy needed to propel electric vehicles are sensitive to extreme temperatures and may be irreversibly damaged or destroyed if the proper procedures are not followed when performing repair and refinish operations. All vehicle repair plans should begin by referencing the original equipment manufacturer (OEM) procedures and following them throughout all phases of the repair. It is critical for the repairer to be fully informed of the necessary processes and precautions; not only to protect the vehicle battery, but to minimize the chance of a life-threatening explosion or fire.
The vehicle’s battery temperature is moderated by utilizing various battery thermal management system (BTMS) technologies, depending on the manufacturer. These cooling and heating systems are designed to maintain the battery temperature within the optimal functioning range, which contributes to the expected performance and lifespan of the battery cells. Electric and hybrid-electric vehicle repairs may often require disconnecting the power sources, thereby disabling the active BTMS and rendering the high voltage battery unprotected from temperature extremes like those that occur when curing the paint in the booth. Even if the BTMS is functional, concerns for battery heat exposure remain, and the repairer must still follow the parameters provided by the OEM to prevent possible thermal damage to the battery system.
Creating a refinishing plan to ensure the vehicle’s battery system is not damaged can be a simple and straightforward process. In basecoat/clearcoat refinish systems, clearcoat curing specifications will determine whether the refinish operation meets the parameters set by the vehicle manufacturer for preventing damage to the battery system. The information in the clearcoat technical data sheets will provide this data.
When assessing the suitability of a selected paint system, it is important to understand key concepts related to force curing in a paint booth:
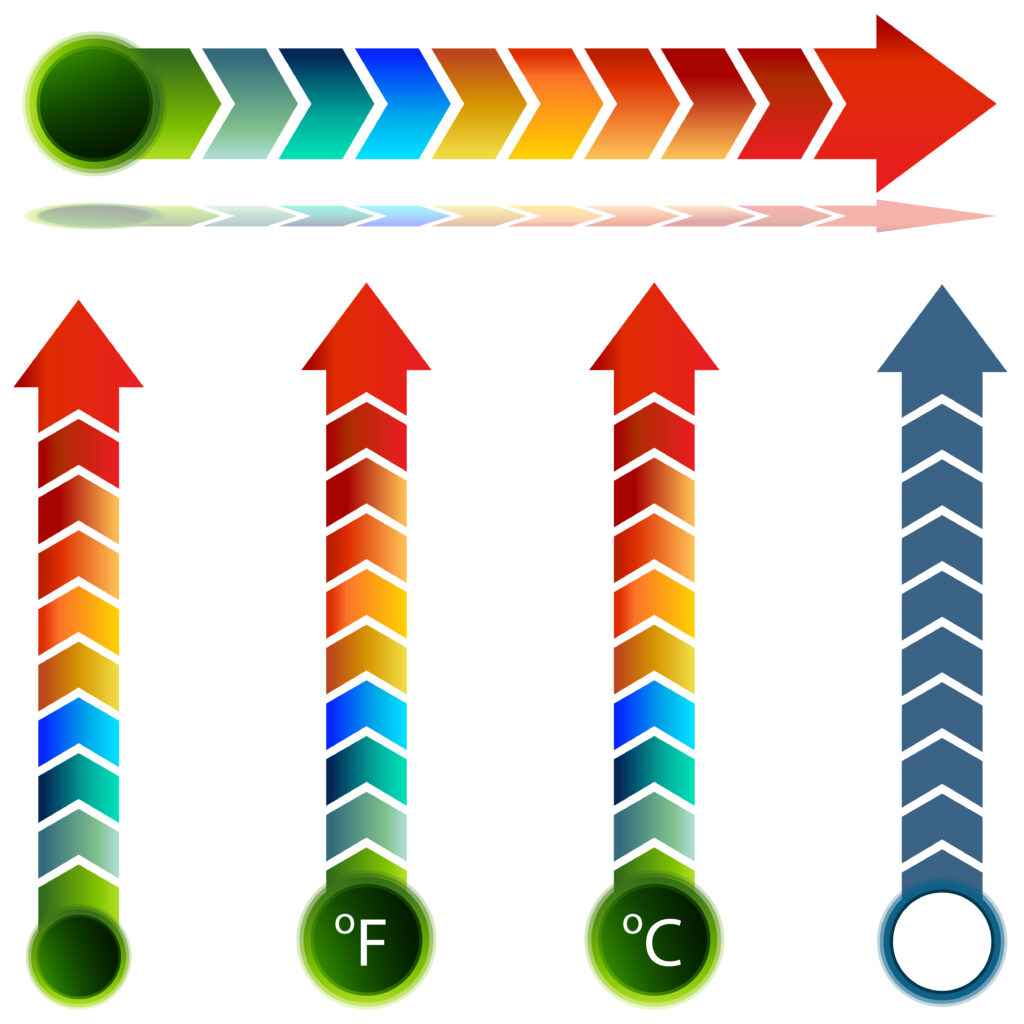
Bake temperature: The temperature at which the booth has been set to cure the paint.
Surface temperature: The temperature of the painted object while baking. The surface temperature is typically 15 – 20°F (8 – 11°C), or more, lower than the set bake temperature.
Ramp time: The time required for the surface (object) temperature to reach the desired curing temperature. Ambient weather conditions and equipment capabilities can cause this time to vary significantly
It is critical to consider these factors when planning the refinish procedure, as they are directly related to the time and temperature parameters the OEM guidelines will provide. After reviewing and understanding the time and temperature parameters set by the OEM, there are often several paint product system selections that can be effective in reducing bake time, temperature, or both. Some clearcoat systems are designed specifically for low bake temperatures or ambient air-dry conditions. Others offer various bake times and temperatures depending on hardener and accelerator selections. Fully review the clearcoat systems available and find the best fit for your desired time and temperature.
Another option to consider is when the vehicle will be painted. Scheduling the electric vehicle (EV) as the last job of the day may allow for an extended dry time at a reduced booth temperature or an overnight drying period at ambient temperatures, which will eliminate the elevated temperature concern. If choosing this option, always ensure the ambient temperature is high enough to cure the paint as curing virtually stops at low temperatures. For further clarification, refer to clearcoat technical data sheets for additional information.
Adjusting long-standing refinish procedures to accommodate technological advancements does not have to be complicated or inherently confusing. The most important part of this challenge is awareness. Creating a repair plan with OEM repair procedures as the foundation is key. Due to the nature of collision repairs, body technicians have long been required to follow the vehicle manufacturer’s procedures. Now, it is time to ensure the refinisher is included in the plan!
This blog was written by Greg Askew, technical services specialist, AkzoNobel Vehicle Refinishes – North America, and has been created in partnership with AkzoNobel.