À mesure que les véhicules électriques à batterie gagnent des parts de marché, la transition technologique des moteurs à combustion interne vers les batteries haute tension (HV) peut nécessiter une approche différente pour de nombreuses opérations de réparation et de remise en état. Les procédures de réparation de longue date peuvent ne plus correspondre aux avancées intégrées dans les nouveaux véhicules. Une telle procédure qui peut nécessiter une réévaluation est la manière dont le système de finition appliqué est polymérisé.
Les températures élevées couramment utilisées pour le séchage forcé d’un système de finition automobile peuvent potentiellement causer des dommages thermiques à la batterie HV. La possibilité que la température de polymérisation en cabine soit trop élevée est quelque chose que les techniciens considéraient rarement, voire jamais, par le passé. Les batteries HV qui stockent l’énergie nécessaire à la propulsion des véhicules électriques sont sensibles aux températures extrêmes et peuvent être irrémédiablement endommagées ou détruites si les procédures appropriées ne sont pas suivies lors des opérations de réparation et de remise en état. Tous les plans de réparation de véhicules doivent commencer par une consultation des procédures du constructeur d’équipement d’origine (FÉO ) et s’y conformer tout au long des phases de la réparation. Il est essentiel que le réparateur soit pleinement informé des processus et des précautions nécessaires, non seulement pour protéger la batterie du véhicule, mais aussi pour minimiser le risque d’explosion ou d’incendie potentiellement mortel.
La température de la batterie du véhicule est régulée par divers systèmes de gestion thermique de batterie (BTMS), selon le fabricant. Ces systèmes de refroidissement et de chauffage sont conçus pour maintenir la température de la batterie dans une plage de fonctionnement optimale, ce qui contribue à la performance attendue et à la durée de vie des cellules de batterie. Les réparations de véhicules électriques et de véhicules hybrides électriques peuvent souvent nécessiter la déconnexion des sources d’alimentation, désactivant ainsi le BTMS actif et laissant la batterie haute tension sans protection contre les températures extrêmes comme celles observées lors de la polymérisation de la peinture en cabine. Même si le BTMS est fonctionnel, les préoccupations concernant l’exposition thermique de la batterie subsistent, et le réparateur doit toujours suivre les paramètres fournis par l’ FÉO pour éviter d’éventuels dommages thermiques au système de batterie.
Élaborer un plan de remise en état pour garantir que le système de batterie du véhicule n’est pas endommagé peut être un processus simple et direct. Dans les systèmes de finition couche de fond/couche transparente, les spécifications de polymérisation du vernis détermineront si l’opération de remise en état respecte les paramètres fixés par le constructeur du véhicule pour éviter d’endommager le système de batterie. Les informations contenues dans les fiches techniques du vernis fourniront ces données.
Lors de l’évaluation de l’adéquation d’un système de peinture sélectionné, il est important de comprendre les concepts clés liés à la polymérisation forcée dans une cabine de peinture :
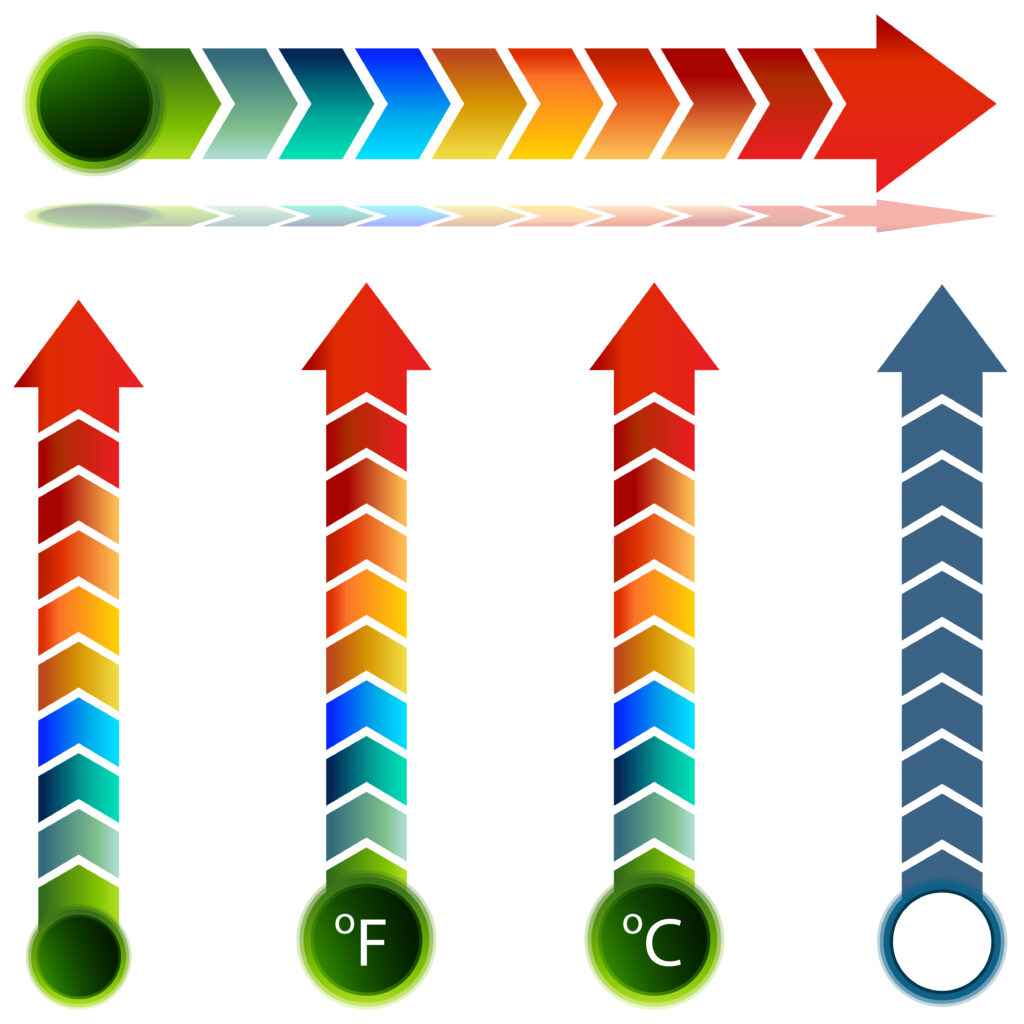
Température de cuisson : La température à laquelle la cabine est réglée pour polymériser la peinture.
Température de surface : La température de l’objet peint pendant la cuisson. La température de surface est généralement inférieure de 15 à 20 °F (8 à 11 °C), voire plus, à la température de cuisson réglée.
Temps de montée en température : Le temps nécessaire pour que la température de surface (de l’objet) atteigne la température de polymérisation souhaitée. Les conditions météorologiques ambiantes et les capacités de l’équipement peuvent entraîner des variations importantes de ce temps.
Il est essentiel de prendre en compte ces facteurs lors de la planification de la procédure de remise en état, car ils sont directement liés aux paramètres de temps et de température fournis par les directives du fabricant d’équipement d’origine (FÉO). Après avoir examiné et compris ces paramètres définis par le FÉO, plusieurs systèmes de peinture peuvent souvent être choisis afin de réduire le temps de cuisson, la température ou les deux. Certains systèmes de vernis sont spécifiquement conçus pour de faibles températures de cuisson ou des conditions de séchage à l’air ambiant. D’autres offrent divers temps et températures de cuisson selon les durcisseurs et les accélérateurs utilisés. Il est important d’examiner en détail les systèmes de vernis disponibles pour trouver celui qui correspond le mieux au temps et à la température souhaités.
Une autre option à envisager est de planifier l’application de la peinture en fin de journée. Programmer le véhicule électrique (EV) comme dernière tâche du jour peut permettre un temps de séchage prolongé à une température réduite en cabine ou un séchage nocturne à température ambiante, éliminant ainsi le problème lié à la température élevée. Si vous choisissez cette option, assurez-vous que la température ambiante est suffisamment élevée pour polymériser la peinture, car le processus de polymérisation cesse pratiquement à basse température. Pour toute précision supplémentaire, consultez les fiches techniques du vernis.
Adapter les procédures de remise en état de longue date pour tenir compte des avancées technologiques n’a pas à être complexe ni déroutant. La prise de conscience est l’élément le plus important de ce défi. Élaborer un plan de réparation fondé sur les procédures de réparation de le FÉO est essentiel. En raison de la nature des réparations après collision, les techniciens en carrosserie doivent depuis longtemps respecter les procédures du fabricant du véhicule. Il est maintenant temps de veiller à ce que le spécialiste en finition soit également inclus dans le plan !
Ce blog a été rédigé par Greg Askew, spécialiste des services techniques, AkzoNobel Vehicle Refinishes – North America, et a été créé en partenariat avec AkzoNobel.